Cargo Cult
Fountain Hills, AZ
|
275
Published: 2024-09-23
Trek 820 mountain bike meets xtracycle Free Radical and the Stokemonkey.
The idea of using a hub motor to create a mid-drive made me smile the first time I saw it. But having the pedals always turn if the motor was running bugged me. I also wanted my next ebike to have a throttle driven by torque sensing of some kind. That's not possible with the conventional Stokemonkey setup. The solution to both problems was a right side drive with a freewheeling crank. Easier said than done, but certainly doable. And as it turned out, Grin was closing out some Stokemonkey parts right about the time I was noodling this over. It took five years of on-again off-again working on it, but it is finally done.
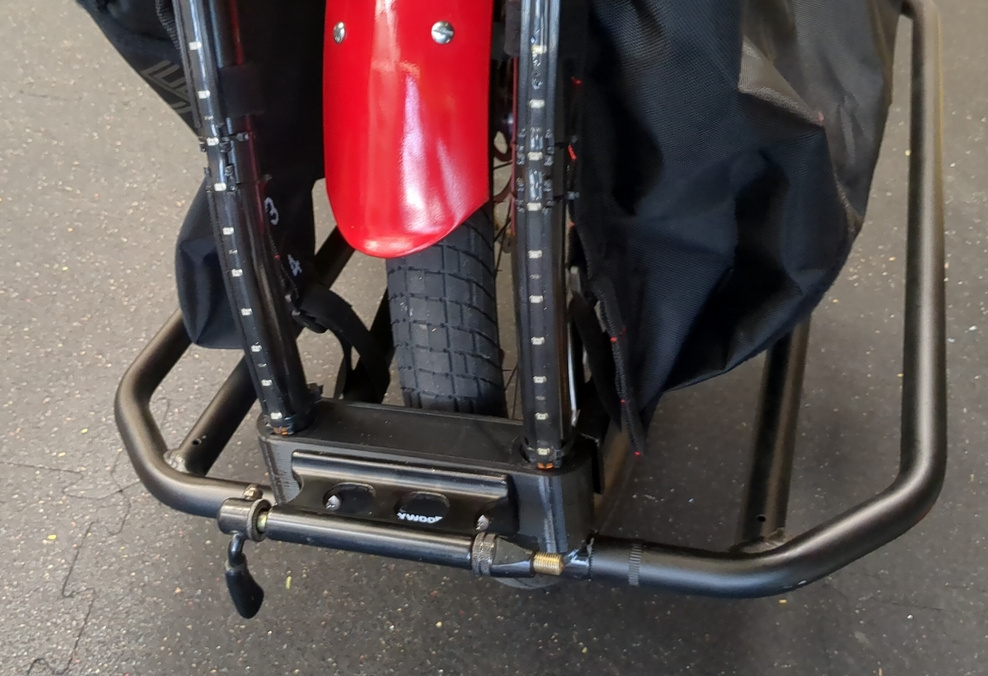
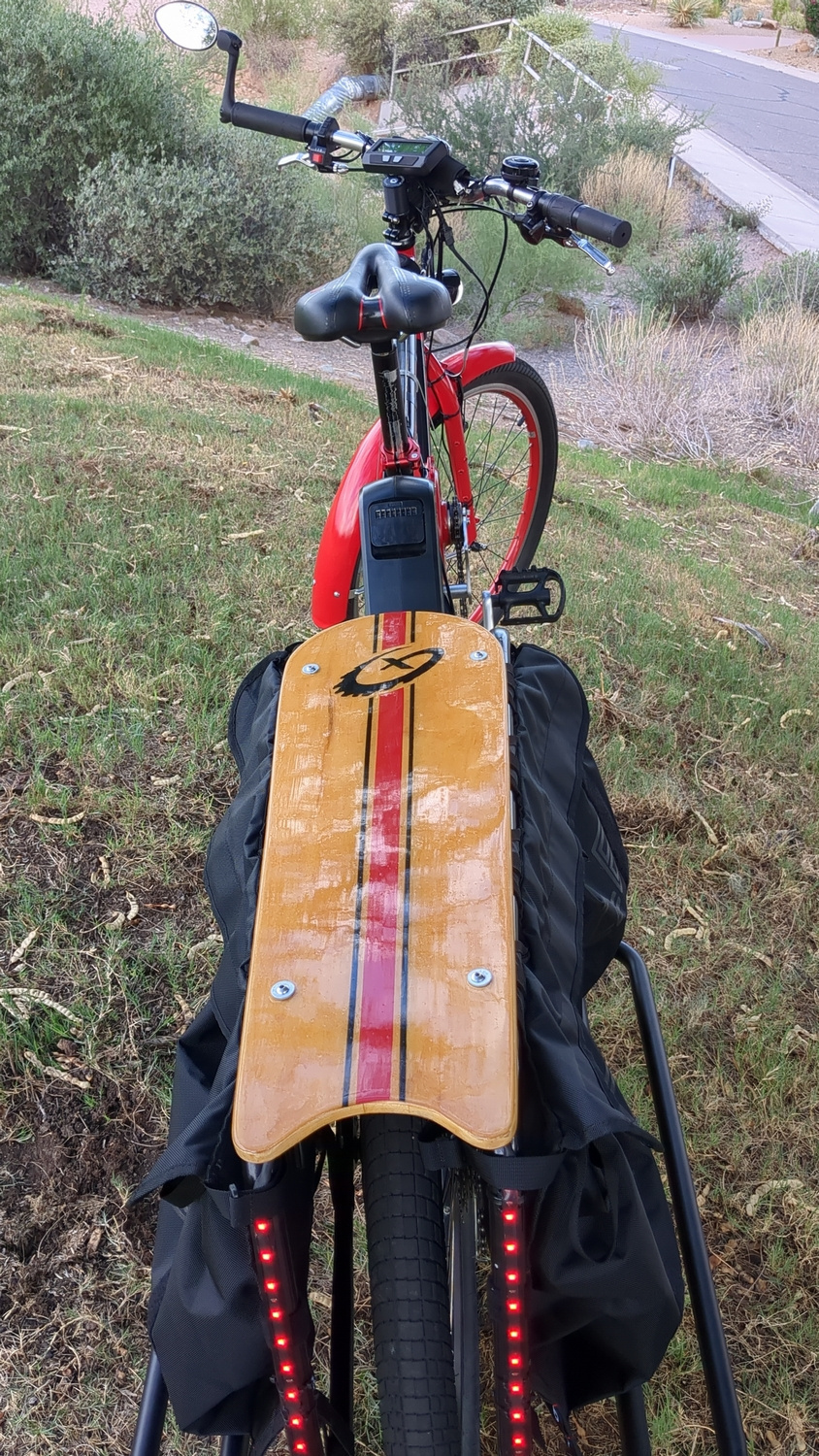

Drive System
The drive system combines an ACS Southpaw freewheel on the Crystalyte motor with a White Industries freewheel on the crank. The outer chainring is driven by the motor, but both chainrings will freewheel on the bottom bracket. In order to mount the left drive freewheel, I needed to replace the motor's freewheel mount with some left-handed threads. So I literally hacksawed the threads off the motor cover and then carefully filed the remaining surface flat. That let me mount a right sided bottom bracket bearing cup to the cover. Right side cups have left handed threads that match the ACS Southpaw freewheel. I have no access to proper machine tools, so I printed drill guides on my 3D printer that centered themselves using the center hole of the motor's cover plate and the bearing cup. For good measure, I bonded the cup to the motor cover with some toughened epoxy. Couldn't hurt. And finally, I made a couple of side plates to engage the flat sides of the bearing cups to help out in case things get loose. Probably overkill. But these motors have a lot of torque.
The system operates at 48v and uses a Cycle Analyst CA3-DPS along with a 25 amp Grinfineon SineWave motor controller. The motor freewheel has a 16T freewheel driving a 46T chainring. The chainring that drives the rear wheel is 50T. Both are made of steel. I think the system would be more efficient if the front motor chainring was larger, but I'm resisting the urge to optimize. The system seems to be doing fine with a 10 mile round-trip in hilly Fountain Hills using about 15wh/mi with moderate (100 watt) pedaling. This is averaging about 18 mph moving speed with starting and stopping included.
I control torque using Grin's Digital Aux switch. Each click increase the torque multiplication 1x ranging from 0x to 8x in nine steps. I use a CA3 analog switch so that I can switch between Class 2, Class 3 and my normal 1000 watt "off-road" mode. I've rigged the middle button on the Digital Aux switch to be a momentary kill to stop the motor while shifting.
This system climbs 18 percent grades in town with no problem at about 10mph.
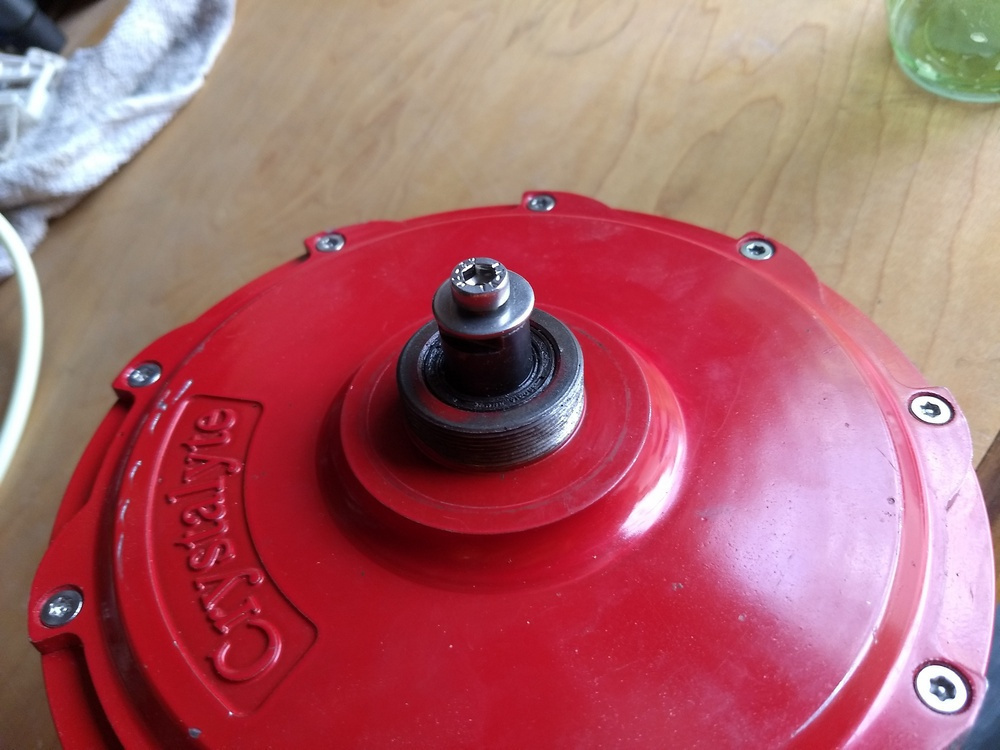
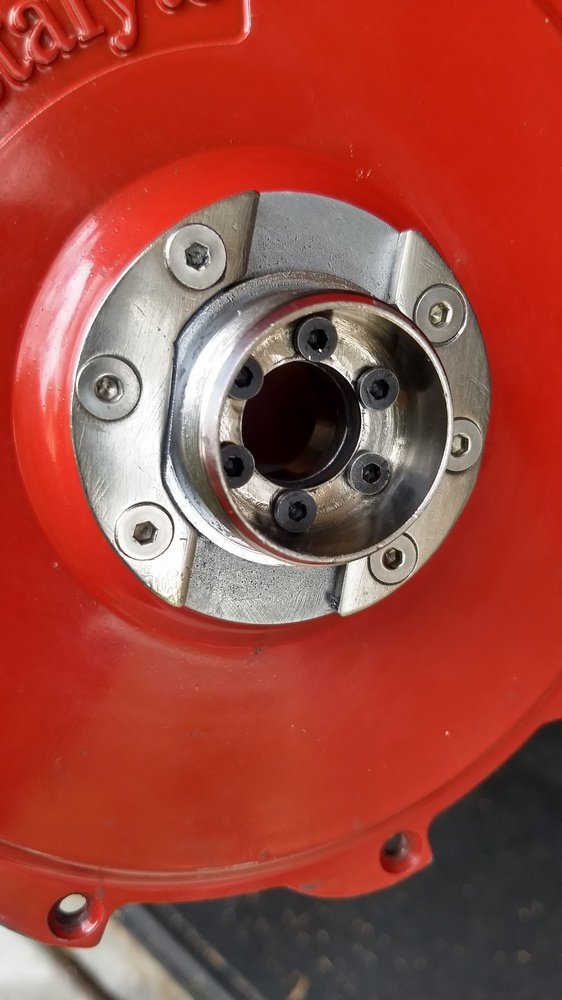
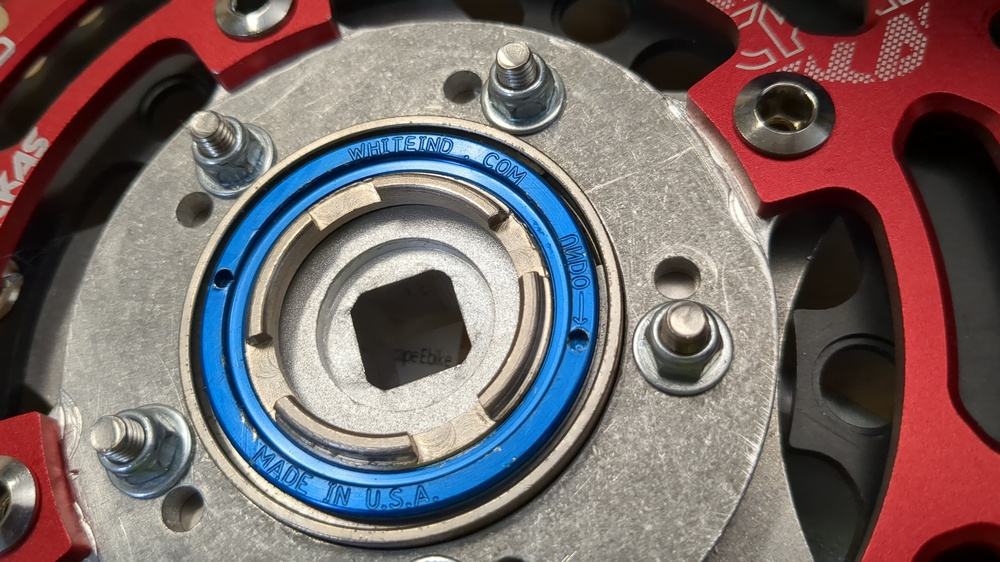
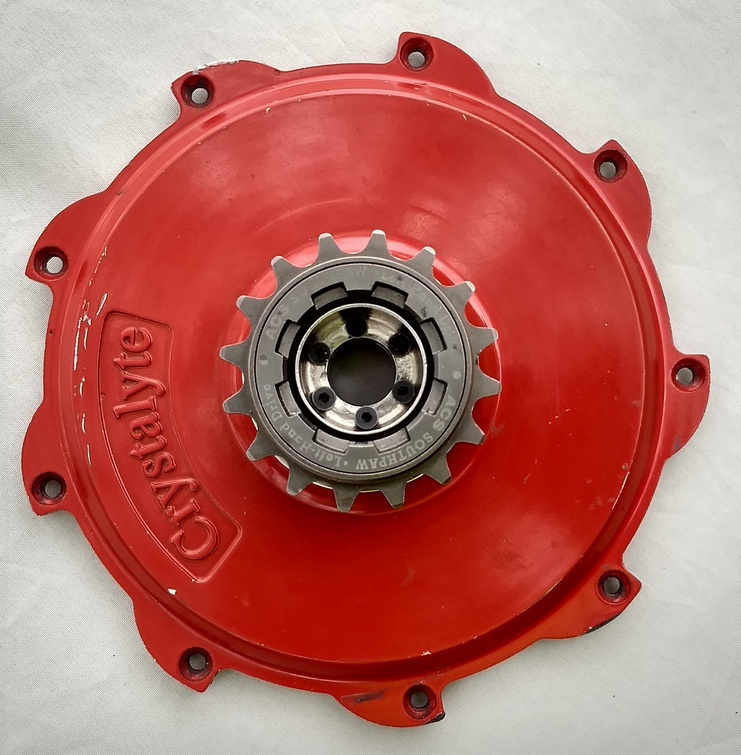
Bottom Bracket
I had to inset the Fischer AG Torque sensing bottom bracket because it didn't provide enough right side offset for the two chainrings. I used a flangeless bearing cup from another used BB so that I could screw the bottom bracket in farther and locate it further to the right. I used liberal amounts of thread locker and then sawed of the supplied BB cup and screwed it in as a lock ring. I 3D printed a spacer ring on the right side (PETG) so that the right side could be tightened up snuggly (not shown).
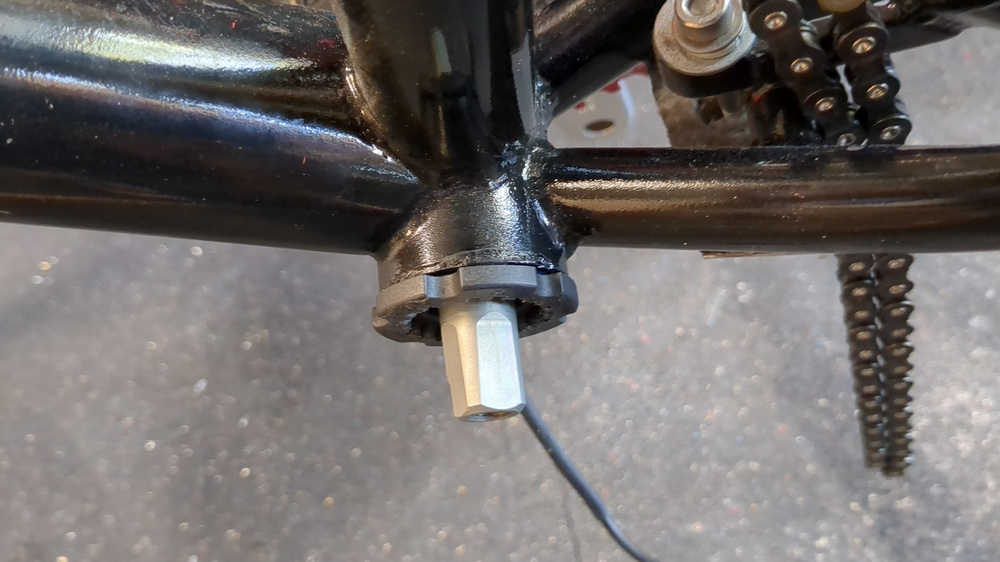
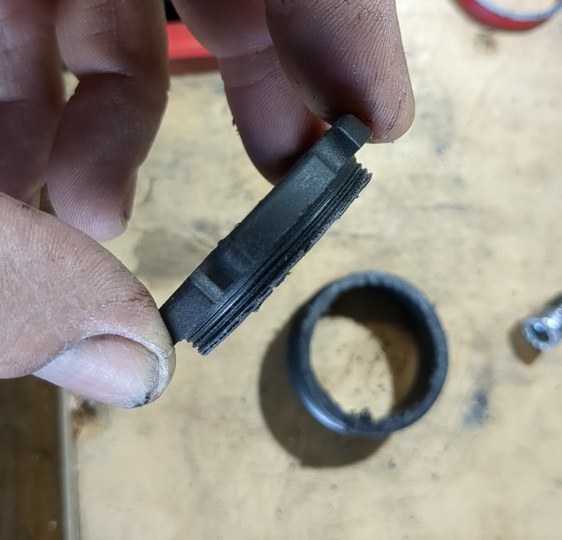
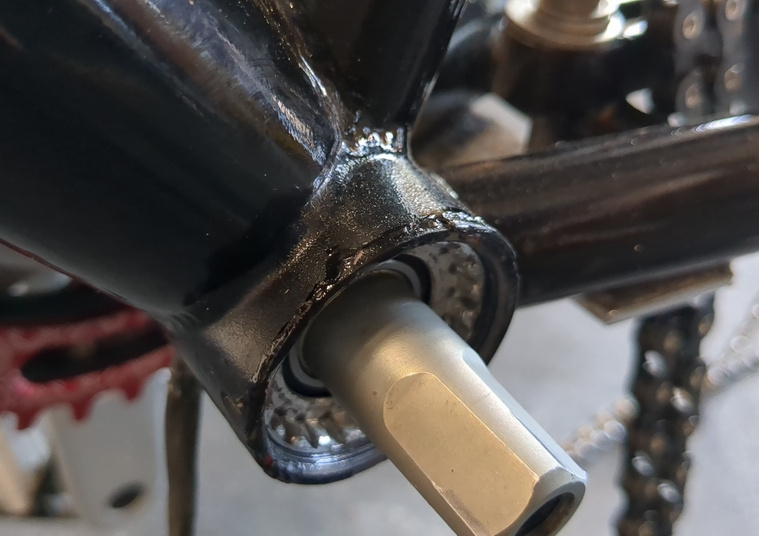
xtracycle Free Radical and Original Mockup
The main components were all found on Craigslist. The Trek 820 is a large tube steel frame mountain bike an the xtracycle was picked up from a gal in Tucson, AZ who had certainly gotten her money's worth out of it. The fork was also from Craigslist and was a bit short - so I lengthened it using some 4130 aircraft tubing. I also reinforced the seatpost tube with some more 4130 tubing that I split and epoxied where I planned to mount the motor.
The original plan was to mount the motor in the rear triangle. The motor does fit there, but the clearances are small. So I moved it to the main triangle. This worked out fine in that it freed up space for the motor controller, battery, and 12v DC downconverter.
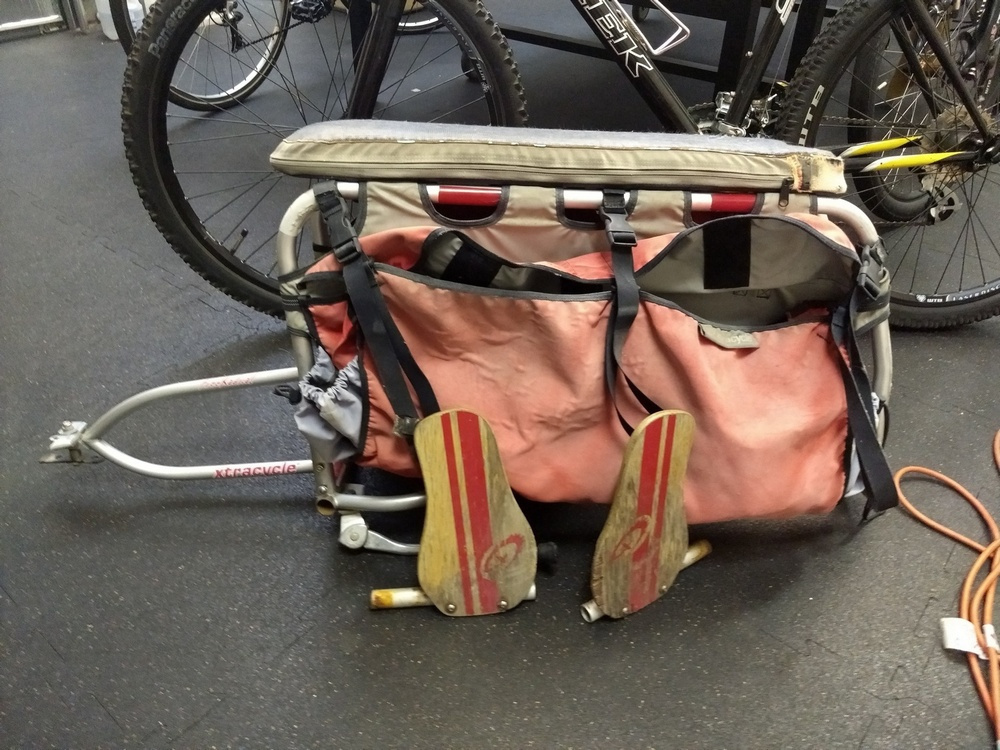
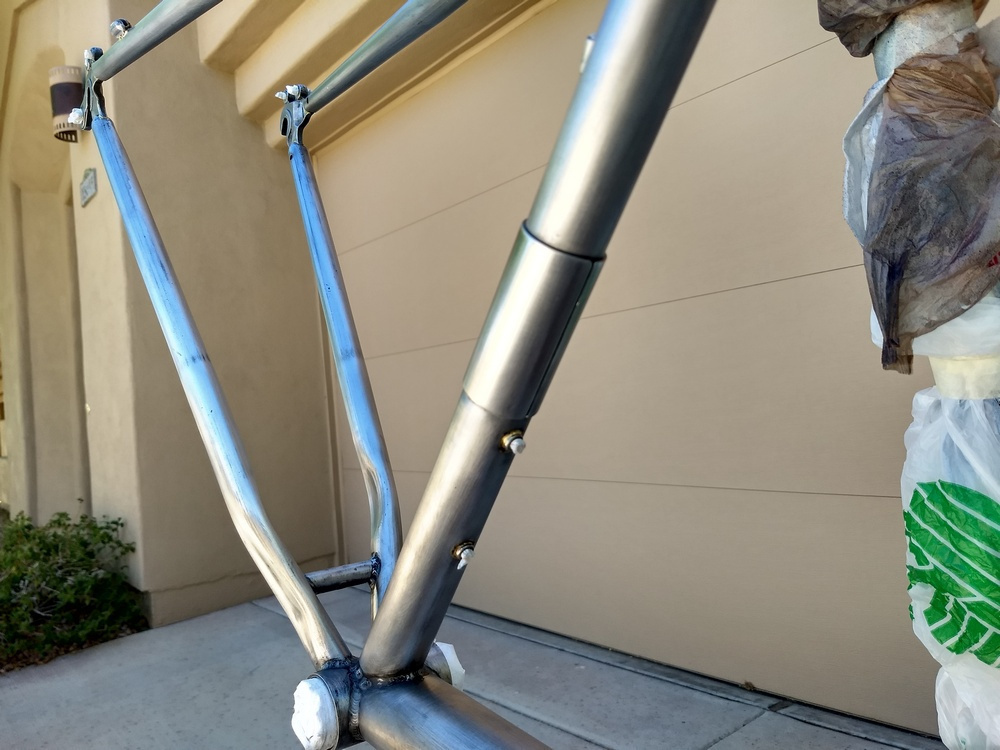
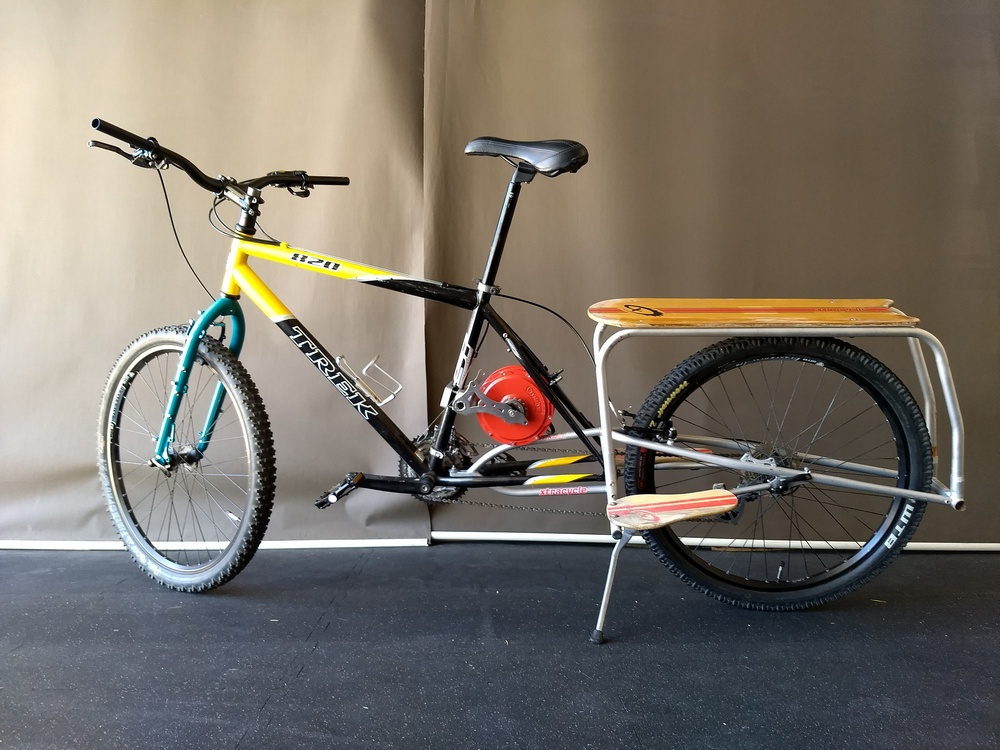

