Torque Arms
Torque arms are used to prevent axle rotation in hub motors. When a hub motor is powered up running, for all the torque that the motor generates spinning a wheel forwards, there is an equal and opposite torque on the axle causing it to rotate backwards.
In a properly engineered hub motor, this torque would be accounted for in the motor design and transfered safely to the frame, (see our Grin All Axle, GMAC, TSM-A5, the Heinzman, BionX, superpestrian etc.) However, in almost all Chinese hub motors, an oversized 12mm or 14mm axle is machined with flats on either side which key into the dropout slot and provides some measure of support against rotation. In some cases this is sufficient to keep the axle secure, in many other cases it is not.
High power systems that generate a lot of torque, or in setups with weak dropouts, the forces present can exceed the material strength and pry the dropout open. When that happens, the axle will spin freely, wrapping and severing off the motor cables and potentially causing the wheel to fall right out of the bike.
To give a sense of the magnitude of these forces, a hub motor with a 12mm axle generating 40 N-m of torque will exert a spreading force of just under 1000lb on each dropout. A torque arm is a separate piece of metal attached to the axle which can take this axle torque and transfer it further up the frame, thus relieving the dropout itself from taking all of the stresses.
Grin's Torque Arm Designs
Grin has been designing and manufacturing torque arms since 2009 when we fully appreciated the severe limitations of the Chinese approach to rely on dropout slots and tight axle nuts to prevent axle spinout. You can see some of our early testing results in this endless-sphere thread here. There are countless styles and geometries of bicycle forks and rear dropout area, and we have done our best at creating flexible torque arm designs that will accommodate this wide array of frame styles.
2023 Torque Arm Models
We released a new torque arm series in 2023 with the V5, V6, and V7 models that all feature a splined interface to a super hard 17-4 staintless steel alloy insert. This results in a more flexible installation and significantly greater spinout strength than our earlier V2, V3, and V4 models. To ensure fitment on your bike, we've made a 1:1 scale .PDF that you can print and cut out of a piece of paper to check for frame compatibility.
![]() |
-NEW- TorqArm_V7Our V7 Torque Arm is designed for motors with regenerative braking, and has a unique and powerful clamping system that puts over 1500 pounds of compressive force on the axle flats to prevent any back and forth wiggle. A solid 11mm (7/16") thick machined of 17-4 hardened stainless steel contains the axle, a sliding plate with two Grade 12 bolts provides compression, and a 25 tooth splined arm interface allows for significant rotational freedom for both front and rear installations. To ensure maximum clamping force and the smallest size, we have slightly different models for 12mm axles and for 14mm axles. |
|
![]() |
-NEW- TorqArm_V6The V6 Torque Arm uses a separate hardened metal insert with a toothed interface allowing for flexible positioning in both front and rear motor installations. It anchors to the bike frame with two hoseclamps and features a swiveling frame bracket to accommodate almost any bike geometry. The hardened 17-4 stainless insert can be rotated in 50 different positions and provides 80% more spinout strength than conventional torque arms. |
|
![]() |
-NEW- TorqArm_V5The V5 Torque Arm has the same hardened metal insert feature as our V6 arm, but secures to the frame via existing fender eyelets rather than using external hose clamps. On bicycles that have fender eyelets in a suitable position near the dropouts, this results in a more discrete and clean torque arm installation. |
2012 Torque Arm Models
![]() |
TorqArm_V4Rear bicycle dropouts are usually thicker and stronger than the front fork dropouts but in cases with shallow vertical dropouts, or with powerful (>1000 watts) motor setups, a torque arm is still important. Our V4 design uses multiple hose clamp slots to secure to the the arm to a seatstay tube. The axle plate can flip directions to accommodate both horizontal and vertical dropouts, while the hose-clamp arm clears up and over most eyelet holes present on the rear. |
![]() |
TorqArm_V3For forks that don't have fender eyelets, or where the fender eyelet holes don't line up, we created up updated variant of the original hose-clamp model with the Ver3 layout. Here, there are small slits for 2 or even 3 hose-clamps to provide extra spinout strength, and the long curved slot in the axle plate allows for for the clamping arm to attach parallel with the fork tube and always intersect correctly. |
![]() |
TorqArm_V2The Ver2 design was engineered to make use of the existing fender eyelet holes that are on most front forks. This can lead to a smaller arm and a tidier installation than using hose clamps around the fork, and we recommend its use whenever there is a suitable eyelet present. This model is OK for medium and low torque motors, but with higher torque levels the axle plate can slide in the long slot of the connecting arm even when the screw and nut are reasonably tight. |
![]() |
TorqArm_V1 / DISCONTINUEDWe developed our first attempt at a 'universal' torque arm design in late 2009. In this model, the arm part was attached to the fork with a single hose clamp, and the the axle plate could pivot to fit different dropout slot angles. When the motor is powered, it tends to rotate the plate clockwise, and with the pivot point on the back this causes it to further 'push' the axle up deeper in the dropout. Notice that if the torque arm is mounted backwards, on the front side of the fork, then it would have the opposite effect and axle torque would tend to pop the wheel out of the dropout. While this design did work and was an improvement over no arm, we ran into failures from the hose clamp in cases where a motor controller had shorted mosfets. The curved hose clamp slot in this design put stress concentration points on the clamp which facilitated the hose clamp tearing in half. As well the contact point to the fork was prone to sliding downwards. As a result we discontinued manufacturing this model in 2010 and do not recommend its usage. There are of course now countless Chinese clones of this bad design being sold by clueless people all over the world. |
Custom Torque Arms
Our V2 to V7 torque arm models were designed to accommodate a wide range of bicycle frame geometries in order to have near universal fit. Many businesses do not require such a broad design as they have only a few select vehicles with a specific fork or dropout shapes. If you are a business dealer looking for a customized torque arm solution perfectly optimized to your frame, then Grin is well equipped to design and fabricate these parts for you.
We keep large stock of stainless sheet material and can go from a design sketch to finished torque arm in your hands in as little as 1 week with quantities as low as 20 pieces. Unlike working with a standard job shops, you'll be dealing with a company that is well versed in all the intricacies and requirements for a hub motor torque arm. Please Contact Us via email if you would like to explore that option.
General Torque Arm Info
Manufacturing:
All of our torque arms are manufactured from raw materials into packaged goods with tight process control at our facilities in Vancouver, Canada. The V2-V4 models use thick ¼" stainless steel plate for the anti-rotation slot, while the V5-V7 models use specially hardened 17-5 stainless for the axle inserts for even greater spinout strength. All models use A4 stainless steel hardware for the various fasteners as well.
Purchasing:
All models of torque arms are all available directly from our Torque Arms store page, from various dealers around the world, and also via Amazon.com for customers in the USA.
V2-V4 Installation:
The images above show the correct installation alignment for the earlier generation models we designed. There are a few important points:
Tighten the 1/4" bolt between the axle plate and the arm as snug as possible. If this nut is loose, then axle can rotate some amount and the bolt will slide in the slot. Though it will eventually bottom out and prevent further rotation, by the time this happens your dropout may already be damaged.
The tolerances on motor axles can vary from the nominal 10mm. The plate may slide on freely with a bit of play, it may go on perfectly snug, or in some cases a small amount of filing may be necessary for the plate to slide on. In situations where the axle flats are a bit narrower than 10mm and you feel play, it is not much of an issue, but you can "preload" the axle plate in a clockwise direction as you tighten everything up.
Many dropouts have quick release "lawyer lips" that come out sideways and prevent the torque plate from sitting flat against the dropout. If this is the case, you will want to be sure to have a washer that fits inside the lip area. We make custom "spacer 'C' washer" for this job, though the lock washer that comes with many hub motors is often about the right width and diameter.
For the hose-clamp model, a small length of heat-shrink tubing over the stainless steel band can make the final installation look more discrete and protect the paint job from getting scratched. We include several pieces of shrink tube with each torque arm package.
Videos
Frequently Asked Questions
The common answer to this question is "yes, you must always have a torque arm installed with any hub motor setup..." The reality is that for many years torque arms were pretty rare in ebike conversions, without issue. But with people pushing the motors to higher power levels, and with the proliferation of weaker alloy suspensions forks, the need for torque arms has grown significantly.
We did a number of dropout and torque arm strength tests in 2009 to better understand the situation, and for those with a scientific bend many of the results were published in this endless-sphere thread.
In a nutshell, axle spinout happens at around 60-90 N-m with most forks. Aluminum dropouts tend to crack and fail catastrophically while steel dropouts will just spread open. The addition of a torque arm can increase this to >150 N-m. The graphs below show some typical axle spinout torque profiles for plate metal and cast aluminum dropouts, with and without the torque arm. Note that these tests are for only one side of the dropout, so the spinout force would double in practice with both left and right dropouts engaged.
If its a rear install, even an aluminum dropout is OK provided that it's plate metal at least 8-9mm thick and you have a 14mm rather than a 12mm axle.
You are sure to always always secure your axle nuts as tight as possible without stripping the threads.
That last point is an important one, because it can easily happen in the course of replacing a flat tire or the likes that the wheel is put back on with only hand-tightened nuts. If the throttle is applied in this state, you'll be guaranteed a spread dropout and spun axle.
For powerful setups (>1000 watts input power), setups with front aluminum dropouts, setups with regen braking, then a torque arm should be used for sure.
For the torque arms we make with the thick ¼" axle plate, one is almost always more sufficient, but of course it never hurts to have two. Installing a 2nd torque arm will be tricky if you have a hub where the cable exits the end of the axle, as you'll need to cut the connectors off the wire and then reattach them.
If you are using a 3rd party torque arm that is made from thinner 1/8" (3mm) metal plate, then we'd recommend doubling up and installing 2 arms.
No it does not matter, the torque arm plates are sized to accomodate a 14mm axle, but will fit a 12mm fine as well. With a 12mm axle, there is a small gap at the top or bottom of the slotted hole, but it is of no consequence and does not affect the spinout retention strength.
A 14mm axle has a much wider flat area and provides more spinout protection, both inside a dropout but especially inside a torque plate. However, a 14mm axle on front forks often leads to interference issues with the large diameter 14mm nut and washers, and it's a bad situation if the washers and nut don't stack up flat against the dropout.
Most rear dropout plates are flat and don't have this issue. For these reasons we tend to spec our orders of rear hub motors with 14mm axles, and the front motors with 12mm so that the axle hardware can fit inside the front dropout cavity. The exception is the new Crystalyte H motors, which are 1/2" (~12.5mm) both front and rear.
In a regular ebike where the motor is torque is always in the forwards direction, the axle only has a backwards torque on it. In practice, the axle will rotate until it has completely bottomed out both against the torque arm and the dropout slot. In a system with regenerative braking, the torque on the axle reverses direction, which can allow the axle to rotate a bit the other way until it bottoms out on the forward surfaces. If there is a sufficient amount of play, this back and forth rocking of the axle can eventually cause the axle nuts to loosen or the axle to wiggle itself out of position.
It can't be overstated how important it is in this case that the axle nuts are thoroughly tightened and that the torque arm plate fits tight on the axle to reduce the amount of 'wiggle room'. It is possible as well to use two torque arms, and preload one in the forwards and the other in the reverse direction.
We don't currently have a "regen specific" torque arm design in production, but do have a few on the drawing board.
If you have metalworking tools then yes, absolutely, and with a custom torque arm designed for your particular frame you should be able to make a tidy single piece arm that makes use of existing eyelets or bolt holes. Some people have also used 10mm crescent wrenches as torque arms in a pinch. There are many great examples on this ES thread.
One important point is that you'll want to make the plate that goes over the axle is at least 5mm (3/16") thick. Most early torque arm designs we saw were made from 1/8" (3mm) steel plate, and even with a snug fit on the axle this doesn't provide all that much anti-rotation strength, just 20-30 Nm more torque than having no torque arm at all.
It's possible to have a custom arm made from two metal plates that "clamp" the axle flats, but if you do this be aware of the strength of the bolts holding the two plates together. We've seen a case of the bolt shearing right in half.
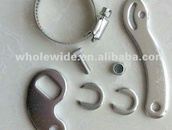
Unfortunately somebody sent a sample of our first universal torque arm design to China in order to have it made cheaply. This happened shortly before we discontinued this model in lieu of the improved Rev2 and Rev3 arm designs. We've since seen this cloned copy proliferate among many China kit suppliers and traders, in ever declining quality, and have with some bemusement had those companies try to sell it right back to us.
If you like our current torque arm designs and want carry them as part of your business, then please contact us. We offer good wholesale volume pricing, and you will be getting a quality-ensured part designed and made in North America by folks who know what they are doing.
Where to Order